In our Acriprint 3D Printer, we had been using the traditional creality style metal extruder in our direct drive extruder hotend system. This extruder (golden) can be seen in the picture below. This particular extruder was chosen firstly because it is available locally off the shelf. Secondly it is made from metal which made it stronger. Thirdly at the time this was the best option available to quickly get the printer operational.
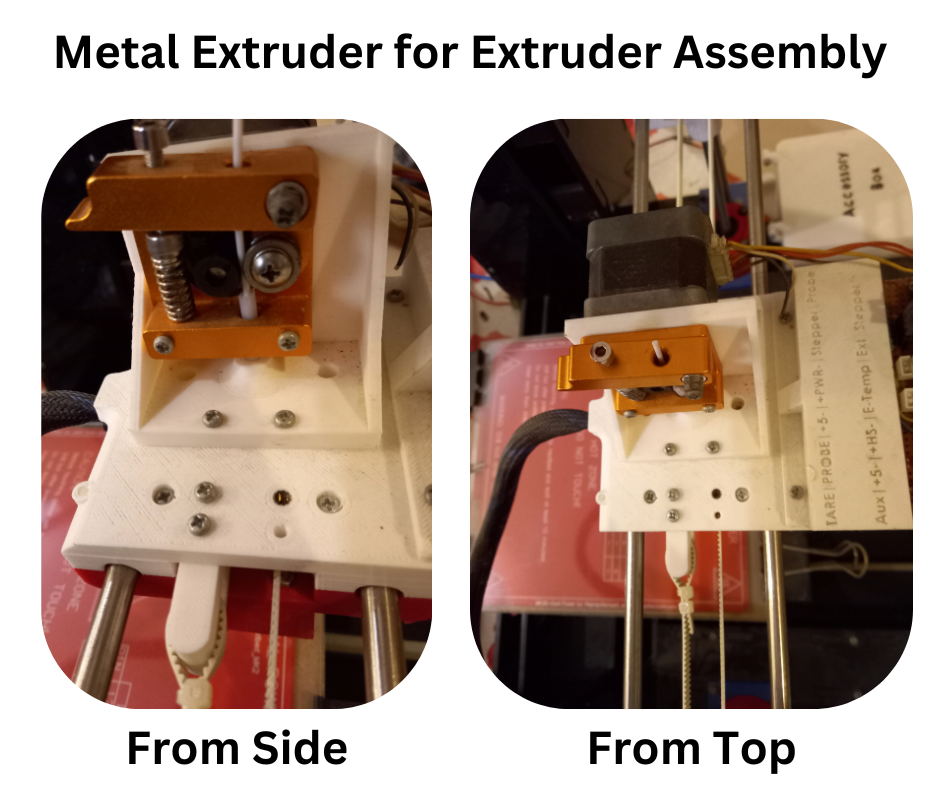
This extruder design although good had some drawbacks that necessitated a redesign. These shortcomings are listed below.
- It is expensive because of its all metal construction
- The extruder requires a 3d printed mount that takes up space because the mount has to be designed around the extruder
- The horizontal style of the tensioner lever arm of the extruder makes it difficult to push it down to change filaments
In addition to the above reasons we wanted to design a 3d printable extruder because it could be designed according to the design of the X carriage. This adds an element of freedom to the design of the entire extruder system. Also since the extruder would be 3d printed, all parts of the extruder except the extruder gear and idler can be easily replaceable.
The following image shows the solidworks design of the new 3d printable extruder.

This design allows the tensioner arm to be positioned vertically which allows space above to easily compress the arm to change filaments. All the extruder parts are 3d printable and use minimum amount of plastic. Therefore this design is cheaper than the store bought metal extruder. And since the parts are 3d printable they can be easily replaced or upgraded.
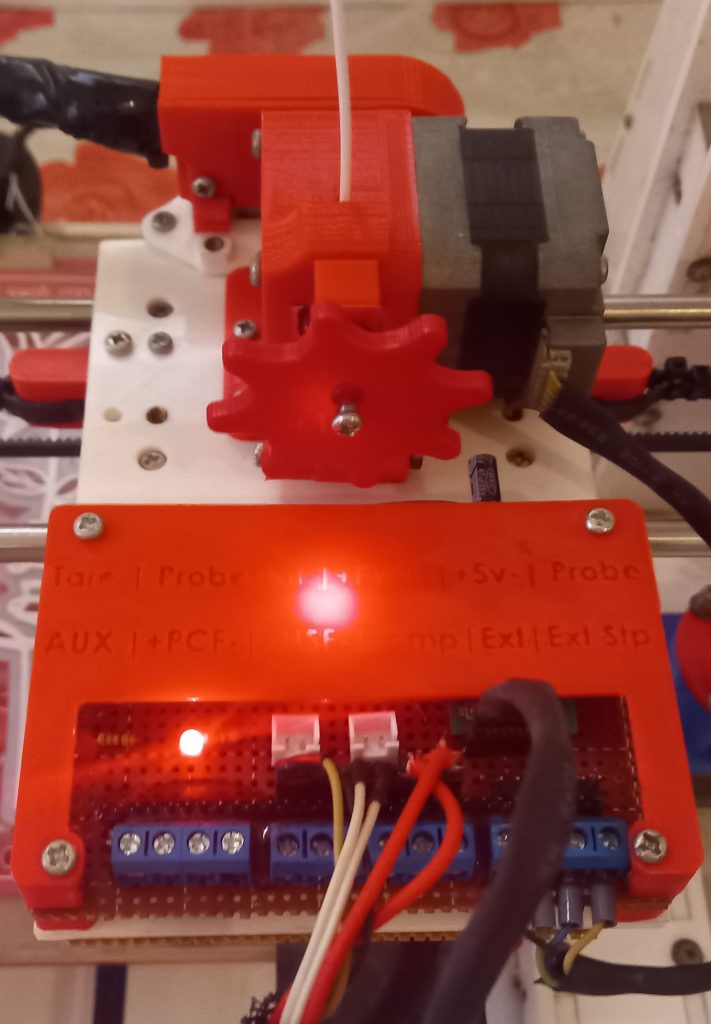
We will be extensively testing this design and will post updates on the performance of this extruder.