Whilst working on our robotic arm project, we also began work on designing a high torque output 3d printable gearbox for a future project. Our requirements were the following.
- Large gearing ratio (more than 20:1)
- Sturdy frame
- Gearing ratio should be changeable
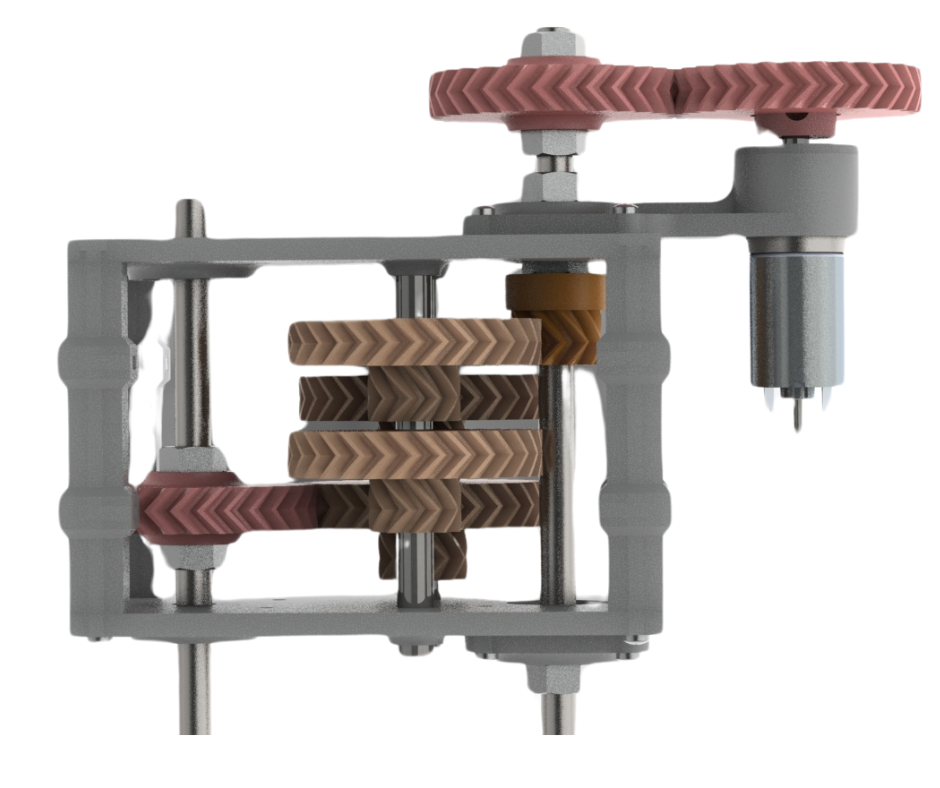
Fig.1
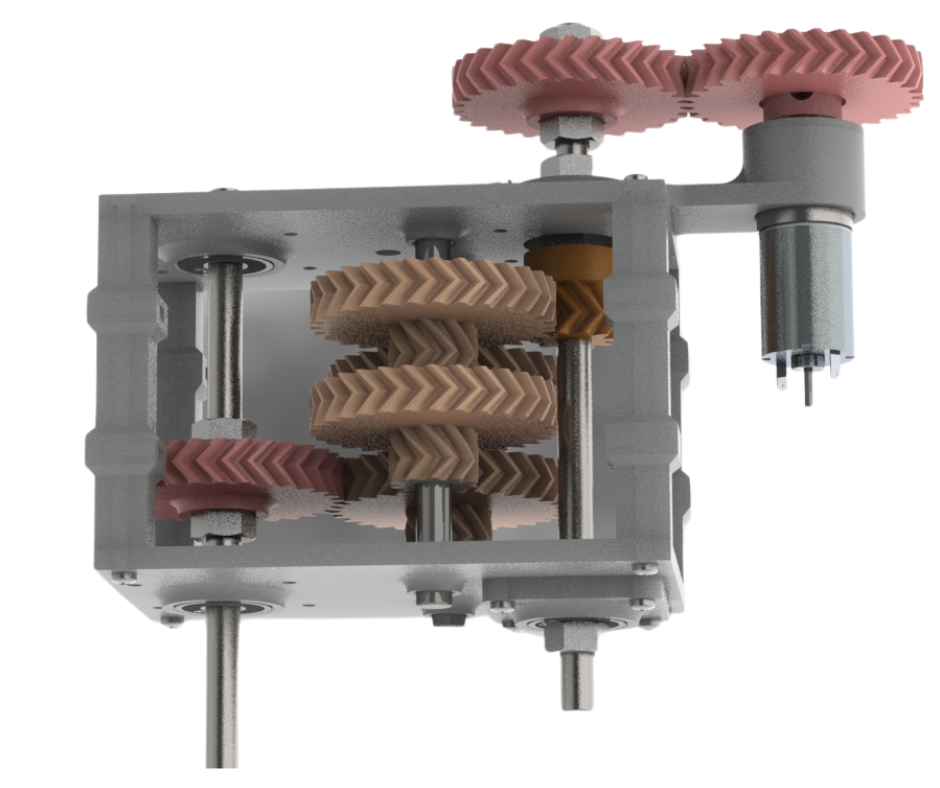
Fig.2
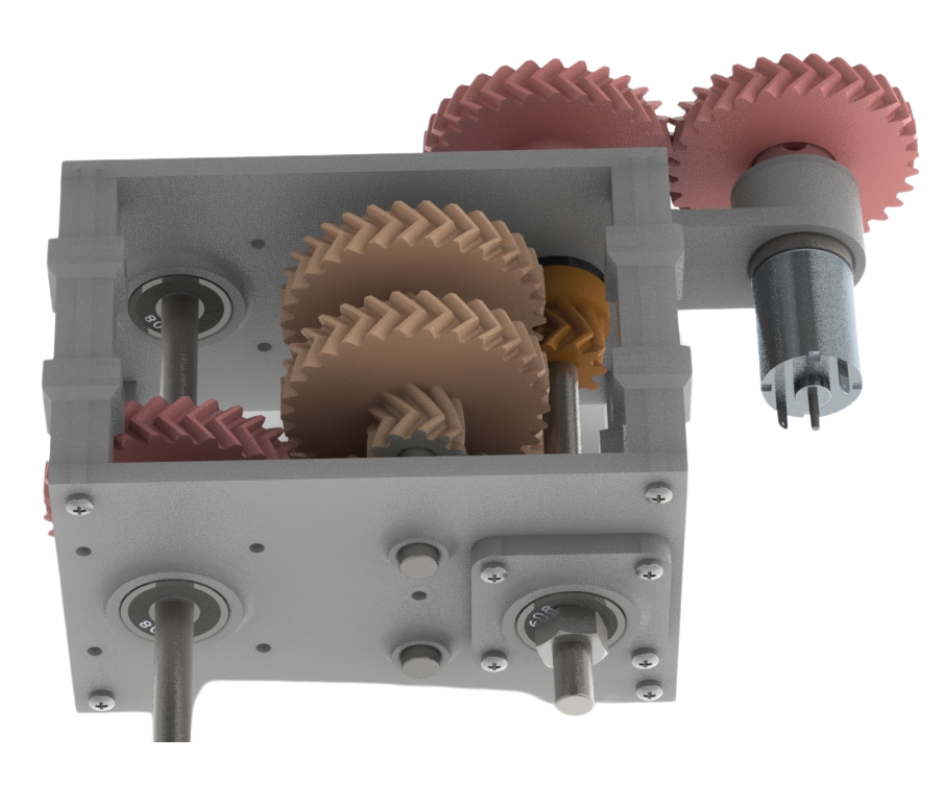
Fig.3
Fig.1 through Fig.3 show our gearbox as designed in Solidworks. Fig.4 shows the different stages in our gearbox. There is the input stage, multiplier stage and the output stage.
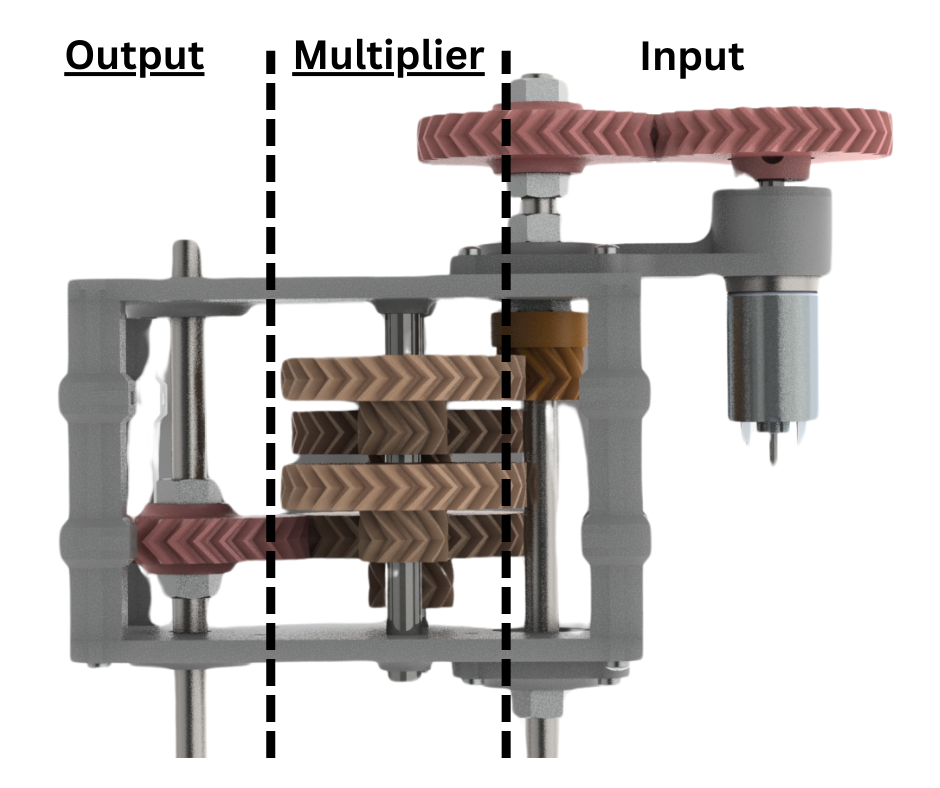
Fig.4
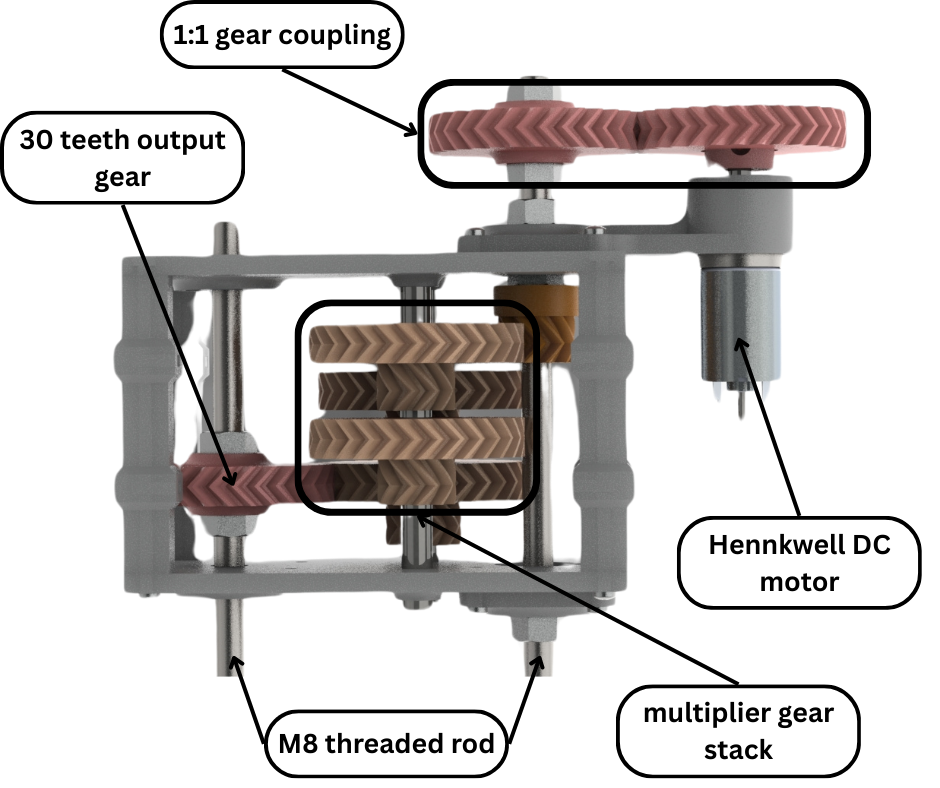
Fig.5
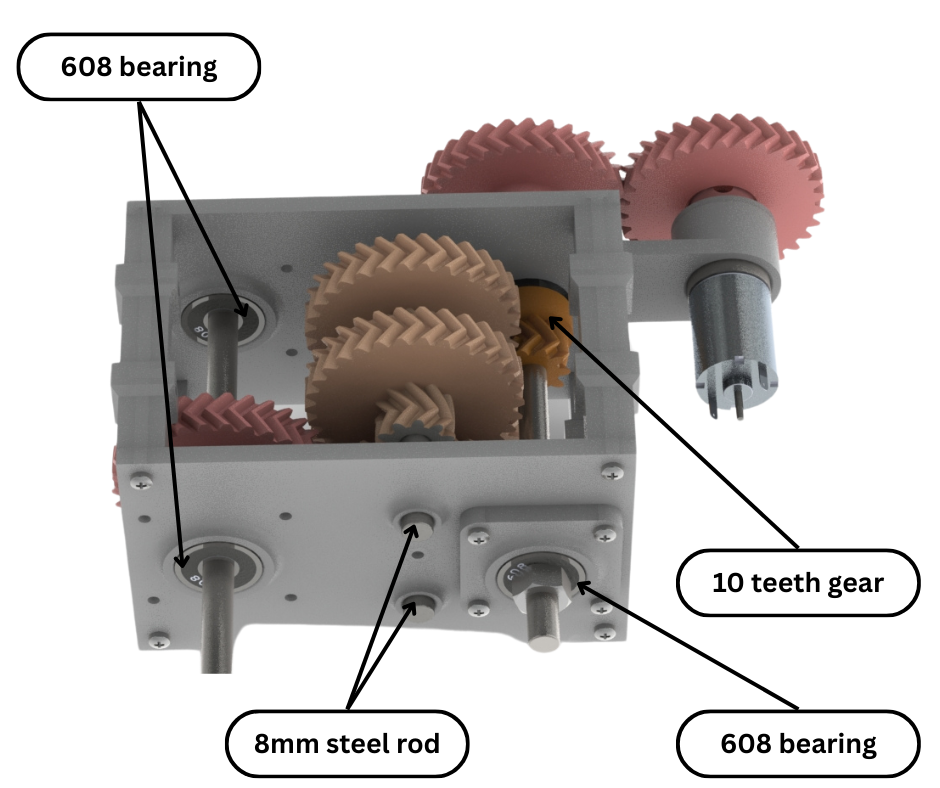
Fig.6
At the input side, there is an M8 threaded rod that goes through two 608 bearings (Fig.6) to keep it aligned and in position. This threaded rod is kept from sliding out by two M8 nuts that are done up against the 608 bearings as shown in Fig.6. This threaded rod is fixed in place but can rotate freely due to the bearings. This is the input shaft for this gearbox. A hennkwell dc motor turns this input shaft via a 1 to 1 geared coupling as shown in Fig.5. As the input shaft turns, a 10 tooth herringbone gear connected to the input shaft as shown in Fig.6 also turns.
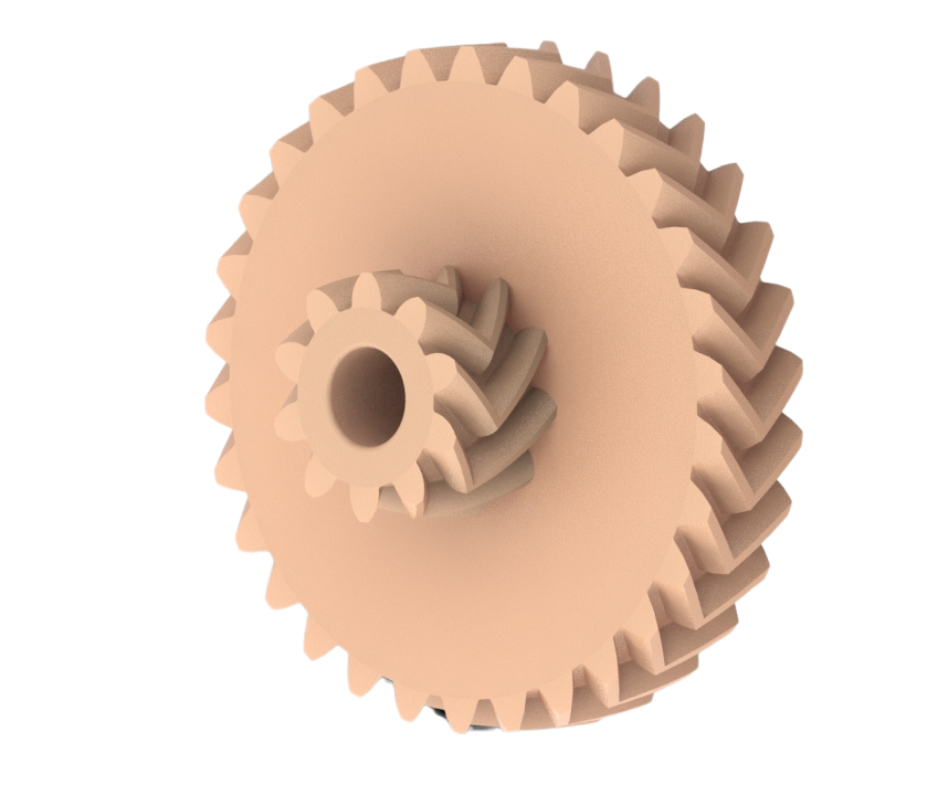
Fig.7
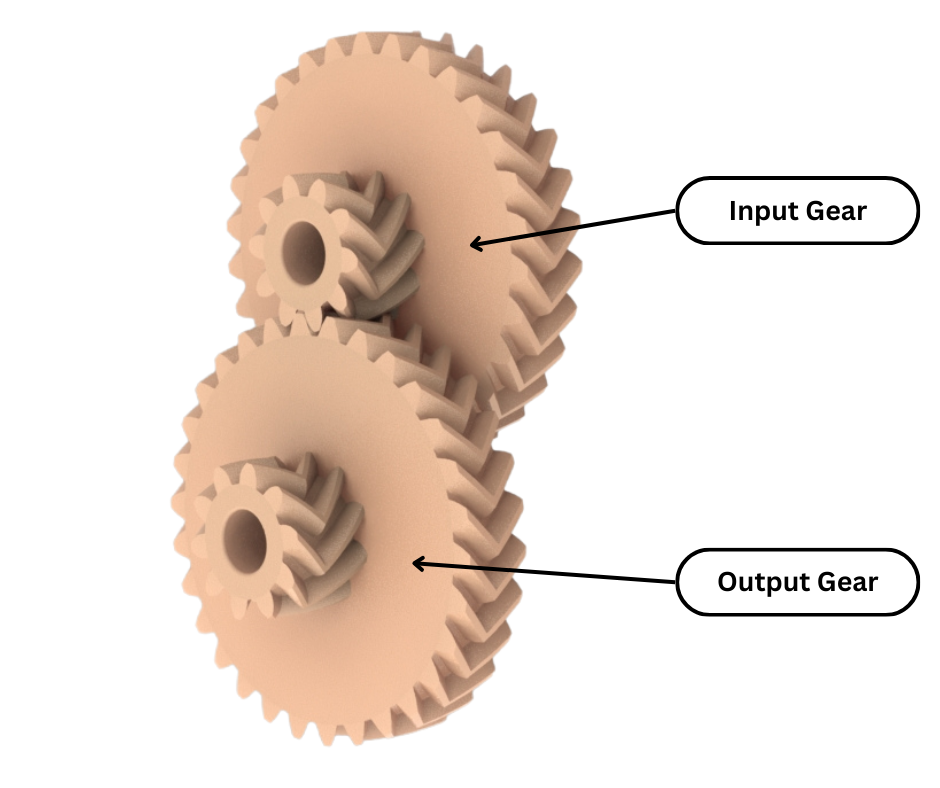
Fig.8
This 10 tooth herringbone gear is coupled to the first gear in the multiplier gear stack in the center multiplier stage. This gear shown in Fig.7 is essentially two gears joined together. A smaller 10 tooth herringbone gear is joined to a 30 tooth herringbone gear. When two such gears are coupled together as shown in Fig.8, the input gear acts as a 10 tooth gear while the output gear acts as a 30 tooth gear. So in this case there is a gearing ratio of 3:1. If another such gear is added to the output then the ratio is increased to 9:1. So the ratio is essentially multiplied by 3 for each gear added to the multiplier stack.
The final gear in the multiplier stack then couples to a 30 tooth herringbone gear connected to the output shaft. An M8 threaded rod is again used as an output shaft and held in place using bearings and M8 nuts.
As can be seen from Fig.1 there are four instances of gear ratio multiplication. Once when a 10 tooth input gear is coupled to the first gear in the multiplication stack. And three times in the multiplication stack. So overall the gearing ratio for this gearbox is 81:1. This means that the input shaft has to turn 81 times for the output shaft to turn once. This also means that the torque at the input is increased 81 at the output.
A lesser gearing ratio is also possible with this gearbox. This can be achieved by simply reducing the number of multiplier gears in the multiplication stack.